A Comprehensive Guide on Engine Compression Testing on a Stand
Engine compression testing is an important diagnostic procedure that offers valuable insights into an engine’s overall performance and longevity. Whether you’re an automobile mechanic, an aspiring automotive enthusiast, or a normal vehicle end-user, understanding how to conduct a compression test is worth mastering.
Engine compression plays a crucial role in the performance and efficiency of an internal combustion engine. It refers to the pressure buildup inside the combustion chamber during the compression stroke of the Engine’s four-stroke cycle. The compression process is essential for proper fuel combustion and power generation. This article aims to shed light on the significance of engine compression, how compression testing works, and how to interpret the results.
The Importance of Engine Compression and How it works
Engine compression is vital for several reasons. First and foremost, it ensures efficient combustion of the air-fuel mixture. When the piston moves upward during the compression stroke, the volume in the combustion chamber decreases. This reduction in volume causes the air-fuel mixture to be compressed, leading to an increase in its temperature and pressure. Higher compression ratios result in greater power output and improved fuel efficiency.
Furthermore, engine compression helps to seal the combustion chamber, preventing any leakage of the air-fuel mixture. Proper sealing ensures that the compressed mixture remains confined within the chamber, allowing for optimal combustion. If there are any leaks, such as worn piston rings or faulty valves, the compression will be compromised, leading to reduced engine performance and potential misfires.
Compression testing is a diagnostic procedure used to assess the health and performance of an engine’s internal components. It involves measuring the compression pressure in each cylinder and comparing the results to the manufacturer’s specifications.
The engine needs to be at operating temperature to perform a compression test. The spark plugs are then removed, and a compression gauge is threaded into the spark plug hole of each cylinder. The engine is cranked several times using the starter motor, while the compression gauge measures the pressure buildup in each cylinder.
The compression readings are typically given in pounds per square inch (psi) or kilopascals (kPa). Each cylinder’s compression reading should be relatively close to one another, indicating a well-balanced engine. A significant variation between cylinders may suggest issues such as worn piston rings, a blown head gasket, or valve problems.
Interpreting Engine Compression Testing Results
When interpreting compression test results, referring to the manufacturer’s specifications for the specific tested engine is important. Generally, a healthy gasoline engine should have compression readings of 125 to 180 psi (862 to 1241 kPa) per cylinder. Diesel engines typically have higher compression ratios, resulting in higher readings.
If the compression readings are consistently low across all cylinders, it may indicate general wear and tear of the piston rings and cylinder walls. This can lead to decreased engine power, increased oil consumption, and possible smoke emission.
On the other hand, if a particular cylinder shows significantly lower compression than the others, it suggests a localized problem. This could be due to a faulty valve, a blown head gasket, or a cracked cylinder head. In such cases, further inspection and diagnosis are required to pinpoint the exact cause of the compression loss.
In some cases, a compression test may reveal abnormally high compression readings. This could be a sign of carbon buildup on the piston or valves, resulting in a hot spot that causes pre-ignition or knocking. It could also indicate incorrect ignition timing or improper fuel octane rating.
Essential Tools and Equipment for Engine Compression Testing
Before proceeding with compression testing, gather the following tools and equipment to conduct a successful test.
1. Compression tester: This device measures the pressure generated by the engine during the compression stroke. Ensure the compression tester is suitable for your testing engine and includes the necessary adapters.
2. Wrenches and sockets: If required, you will need a set to remove and reinstall spark plugs and access other engine components.
3. Safety goggles: Protect your eyes from potential debris or splashing fluids during testing.
4. Use gloves to protect your hands from hot surfaces and improve your grip while handling tools and equipment.
Safety guidelines to observe while carrying out compression testing.
Safety should always be a top priority when working with engines. Before starting the compression testing process, follow these safety precautions:
1. Allow the engine to cool down before initiating any testing procedures. Working with a hot engine can lead to burns.
2. Wear safety goggles and gloves to protect yourself from hazards.
3. Disconnect the battery by removing the negative terminal to prevent accidental starts.
4. Ensure the engine is securely mounted on the stand to prevent movement or tipping during testing.
5. Keep a fire extinguisher nearby, Have a fire extinguisher readily available in case of any unexpected fires.
Setting up the Engine compression test
Properly preparing the engine before compression testing is important to obtain accurate and reliable results. Follow these steps:
1. Clean the eEngine Remove any dirt, debris, or oil residue from the eEngine’sexterior. This allows for better visibility and prevents contaminants from entering the engine during testing.
2. Check the engine oil level: Verify that the engine has the right oil level. Low oil levels can affect compression readings.
4. Disable the ignition system: Disconnect the ignition coil or remove the distributor cap to prevent the engine from starting during the compression testing.
5. Warm up the eEngine Start the eEngineand allow it to reach normal operating temperature. This helps ensure consistent results and reduces the risk of thermal expansion affecting the readings.
6. Disable the fuel system: Either disconnect or remove the fuel pump relay to prevent fuel from entering the engine during testing.
Spark Plug Removal and Inspection
The spark plugs play a crucial role in the compression process, and their condition can provide valuable information about the eEngine’sperformance. Follow these steps to remove and inspect the spark plugs:
Step 1
Identify the spark plug locations: Most engines have one spark plug per cylinder, arranged in a specific firing order.
Step 2
Remove the spark plug wires: Gently disconnect the spark plug wires from the spark plugs by firmly gripping the boot and pulling it straight off. Avoid pulling on the wire itself to prevent damage.
Step 3
Clean the spark plug area: Use compressed air or a soft brush to remove dirt or debris around the holes. This ensures a clean working area and prevents foreign substances from falling into the cylinders.
Step 4
Remove the spark plugs: Use a spark plug socket and ratchet to loosen and remove each spark plug from the engine.
Step 5
Connect the compression tester to the spark plug hole. Ensure a tight and secure fit to prevent any air leakage during testing. Use the appropriate adapter or fitting if required.
Step 6
Repeat the process: Repeat steps 2 and 3 for each cylinder in the engine. It is important to test all cylinders to obtain a comprehensive assessment of the Engine’s compression.
How to perform Engine Cranking and Pressure Measurements
1. Disable the ignition system: Disconnect the ignition coil or remove the distributor cap to prevent the engine from starting during testing. This ensures the engine will only turn over without firing.
2. Crank the Engine Use the starter motor or a hand crank to turn the engine over. Follow the engine manufacturer’s instructions for cranking the engine. The engine should be cranked for a specified number of revolutions, such as four or five.
3. Observe pressure readings: As the engine cranks, the compression tester will display the pressure readings. Please take note of the readings for each cylinder and compare them to the engine manufacturer’s specifications.
4. Record the measurements: Write down the pressure readings for each cylinder. This information will help you evaluate the overall compression health of the engine and identify any significant variations between cylinders.
5. Repeat for accuracy: Repeat steps 1 to 4 for each cylinder in the engine, ensuring consistent cranking speed and technique for accurate and comparable results.
Repeat Testing for Accuracy
To ensure the accuracy of your compression test results, it is advisable to repeat the testing process.
Repeat the entire testing process. Disconnect the compression tester from the first cylinder and repeat the steps outlined in sections 3.2 and 3.3 for all cylinders; once you have obtained measurements for all cylinders, compare the readings. Look for any significant deviations between cylinders, indicating potential issues, such as worn piston rings or valves.
Analyze results and Consult the engine manufacturer’s specifications or a reliable reference source to interpret the compression readings. Evaluate the readings about the expected range for your engine model.
If there are any significant discrepancies in the compression readings or if you suspect inaccurate results, consider retesting or seeking professional assistance.
Common Challenges Encountered in compression testing and Solutions
1. Low compression readings:
Compression readings consistently low across multiple cylinders could indicate worn piston rings or cylinder wall damage.
Solution: Perform a wet compression test by adding a small amount of oil to the cylinder. If the readings improve, it suggests worn piston rings as the cause.
2. Inconsistent readings:
If compression readings vary significantly between cylinders, it may indicate valve problems, such as worn valves or valve seat leakage. Solution: Performing a cylinder leakage test can help identify the specific cause.
3. Compression leakage:
Leakage can occur through various points, including worn valves, piston rings, or a blown head gasket.
Solution: A cylinder leakage test can pinpoint the location of the leakage and guide repairs accordingly.
4. Unexpectedly high compression readings:
Higher-than-normal compression readings may indicate carbon or excessive carbon deposits on the valves or piston crowns. This can affect engine performance and may require decarbonization or valve cleaning.
If you encounter persistent issues or are unsure about the test results, it is advisable to seek professional assistance. Certified mechanics possess the expertise and specialized tools to conduct comprehensive engine inspections and accurately diagnose complex problems.
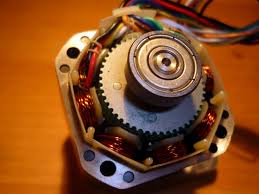
Conclusion
In conclusion, a regular engine compression test is a fundamental aspect of engine maintenance that should not be overlooked. By incorporating this diagnostic procedure into your regular maintenance routine, you can effectively monitor the health of your engine and detect potential problems before they escalate into more severe issues.
Regular compression testing serves as a proactive measure to identify and address problems such as worn piston rings, valve issues, or head gasket failures. By monitoring compression levels over time, you can establish a baseline for your engine’s performance and track any changes or deviations. Any significant decrease in compression readings can indicate potential issues that require attention.
Detecting problems early on through compression testing allows you to take prompt action and implement necessary repairs or maintenance procedures. By addressing these issues at an early stage, you can prevent further damage to your engine and avoid costly repairs down the line. Furthermore, resolving problems promptly helps to maintain the overall efficiency and performance of your engine, ensuring optimal power output and fuel efficiency.
In addition to the diagnostic benefits, regular compression testing also provides peace of mind for vehicle owners. It offers assurance that your engine is operating within its expected parameters and can help identify any underlying issues that may affect reliability or safety.
Read Also: Detailed Classes of Engines Used in Modern Vehicles
It is important to note that compression testing should be performed in conjunction with other routine maintenance tasks and inspections recommended by the engine manufacturer. This comprehensive approach ensures that your engine remains in optimal condition, prolonging its lifespan and enhancing its overall performance.