All You Need to Know About Aircraft Piston Engines: Operation, Parts, Types.
In a previous article, I discussed the use and operation of aircraft gas turbine engines in detail. Those engines are almost synonymous with aircraft engines. However, piston engines – the kind of engines used in cars and other automobiles – are also used in some aircraft. Piston engines are able to provide electricity (in some cases) and torque to drive the propeller(s) which produces thrust for the aircraft. They are used for light aircraft and are unsuitable for use in airliners as they would operate inefficiently for such a range of flights.
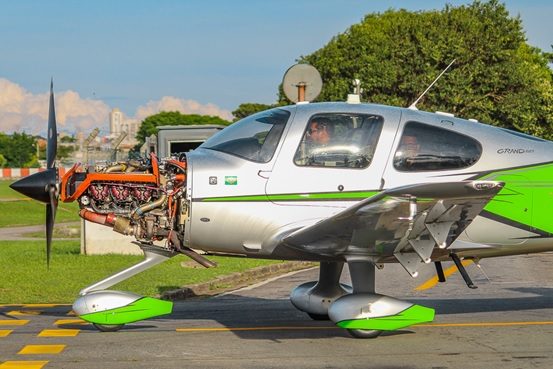
Prior to the early 20th century, many attempts had been made to produce heavier-than-air aircraft, aircraft that could actually have a practical use. This was not possible with the use of steam engines, external combustion engines which had been tried but were found to be too heavy and impractical in other ways. Then came the realization that piston engines could be of great benefit to aviation. In contrast, these were internal combustion engines and were found to give improved efficiency.
Although gas turbine engines were later found to give even more thrust power needed, piston engines are still being used today. This is especially in lighter aircraft which prove to be more efficient based on their flight range. The type of piston engine which will be discussed in this article is a reciprocating piston engine.

We will look at:
- Components of piston engines and their workings.
- The operation of the overall piston engine.
- Types of aircraft piston engines
Components, Subsystems of Piston Engines and their Workings.
Apart from the main parts that are involved in the piston engine’s four-stroke cyclic operation, many other components and smaller systems contribute to the effective operation of the engine system as a whole.
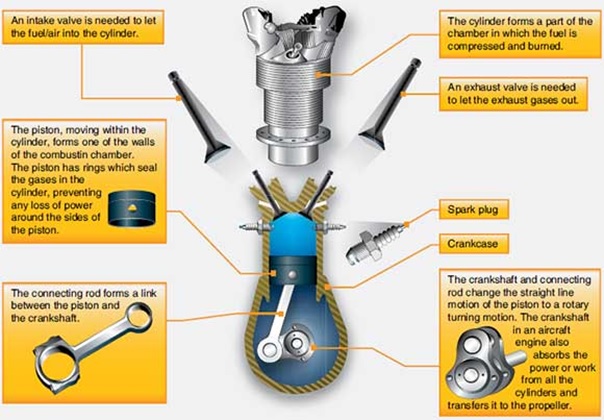
The basic elements of (aircraft) piston engines are:
- Crankcase:
This is the main frame of the engine. It is typically made in 2 halves for ease of maintenance/installation. It houses the crankshaft’s main bearings, supports the cylinders, and has faces to which other engine casings can be mounted and with which the engine can be joined to the aircraft. The crankcase must have adequate rigidity so that the alignment of the crankshaft and its bearings are maintained. The incorporation of transverse bearing supports, one for each bearing, contributes to this rigidity.
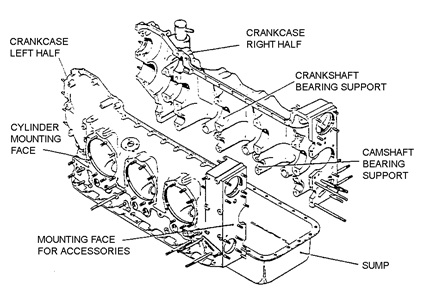
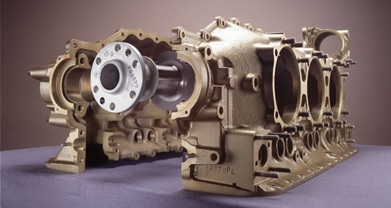
The two halves of the crankcase are held together by a series of long through bolts that pass through them below and above the crankshaft, as well as short flange bolts that connect the top and bottom flanges. The flanges and bearing surfaces must be accurately machined so that the two halves fit perfectly together. The surfaces have direct metal-metal contact with each other. The setup of the crankcase may be such that the crankshaft lies at the center of the two halves such that the main bearings are divided equally between the two halves. It may also be such that the main bearings are on a single side, where the cylinders are placed. The latter option allows for inspection of the crankcase without bearing disruption.
The combination of the crankcase, the sump, and the accessory housing form a sealed container for the lubricant. These components are typically made of light and strong alloys such as cast or forged aluminum alloys. The crankcase is susceptible to bending moments and other mechanical stresses. The bending moments are brought about as a result of the unbalanced centrifugal forces exerted by the rotational crankshaft. These bending moments are continually changing in direction and magnitude as the crankshaft rotates. The crankcase must be so stiff that these bending moments do not cause significant deflections.
The crankcase has three main sections namely, the nose section, the power section, and the accessory section. If the engine is super or turbocharged, there might be an additional section to this effect. The power section is the main section of the crankcase. At its center are the crankshaft’s main bearings. Cylinder pads are surfaces on the power section which serve as a base to which the cylinders can be mounted using studs, cap screws, or bolts. Some manufacturers use a combination of studs and bolts to each cylinder base flange to the cylinder pad.
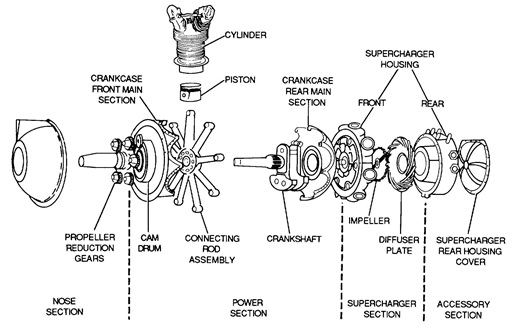
If there is a reduction gearbox (for the propeller) in the engine, the nose/ front end of the crankcase will experience additional forces. Centrifugal and gyroscopic forces will be exerted on the crankcase especially if the aircraft performs many maneuvers and the propeller is large. To combat this, a large centrifugal bearing is used in the nose section of the crankcase.
A governor is a device that controls the speed and blade angle of the propeller. It can be mounted at the back end of the crankcase, although this can be problematic installation-wise, especially if the propeller is hydraulically operated. Ideally, the governor should be mounted at the crankcase nose where it can be closer to the propeller. This acts to shorten the distance the oil travels in getting to the propeller.
Mounting lugs can be found at the sides of the rear end of the crankcase or the base of the crankcase, i.e., a bed mount. In a radial engine, they are found at the diffuser. They are the means by which the engines can be fitted to the engine nacelles (for a multi-engine aircraft) or to the fuselage. The mounting lugs may be fixed to the crankcase (or diffuser) or detachable to allow for an adjustable engine mount.
The mounting assembly must be extremely strong to ensure that the engine as well as the propeller are in appropriate positions at all times in flight. Additionally, elastomeric shock mounts are to be incorporated to absorb any vibrations from the engine before they can get transmitted to the airframe.
- Crankshaft:
This is the backbone of the engine. A connecting rod links the piston to a crankshaft which rotates through 180° every time the piston performs a stroke. Thus, after a complete cycle which comprises 4 strokes, the crankshaft would have rotated through 720°. There is typically one throw for each piston except in radial engines where multiple pistons are arranged around and connected to a single throw. Also, in a horizontally opposed engine, two pistons are connected to a single pin.
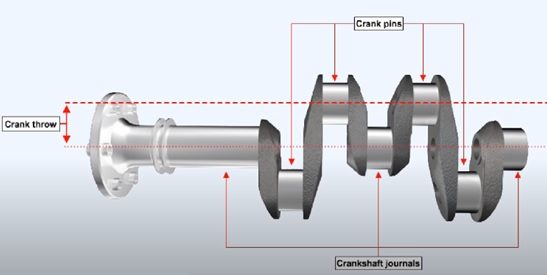

The crankshaft converts the linear motion of the piston to rotary motion which is used to provide useful work. This useful work is in the form of torque which is used to drive the propeller and the accessory gearbox(es). The crankshaft will continuously rotate until the engine is turned off. The journals are the main part of the crankshaft and are supported by the crankcase main bearings. Together with the bearings, they define the rotational axis of the crankshaft. The distance between the centreline of the crankshaft’s journal and that of the crankshaft pin is called the throw. The stroke of the engine is double the crank throw. Alternatively, the throw is a combination of a single crankpin and two crank cheeks.
The crankshaft extends at the front and rear ends of the crankcase. At the front, it is attached to the propeller by means of a propeller mounting flange (in a direct drive engine). At the back, it is attached to a large gear that drives the camshaft, as well as other gears. The journals and crank pins are made hollow, for weight reduction purposes and in order to allow lubricant to pass through. They are also nitrided to obtain hard and durable bearing surfaces.
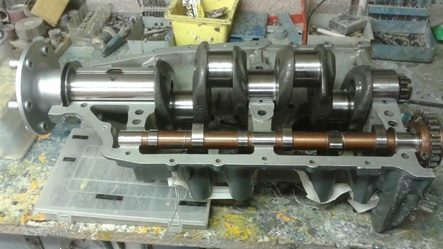
Crankshafts must be well-balanced so as to curb excess vibration. This is achieved by the use of counterweights which are carried on extended crank cheeks. During manufacture or maintenance, static balance is achieved by placing the crankshaft on knife edges and cutting away some of the counterweights until the crankshaft is balanced on the knife edge. Some crankshafts use movable counterweights called harmonic dampeners to achieve dynamic balance. This help to reduce some torsional stress resulting from the power pulses applied to the rear part of the crankshaft. The (steel) weights are pendulous so their resonant frequencies can easily be determined based on the distance they swing either way. These frequencies correspond to the power pulses and can be tuned so that their oscillations can be out of phase with that of the power pulses.
Additionally, crankshafts must not be too long and must have a sufficient number of supporting bearings so that resonance can be avoided as this can lead to very poor performance. Excess vibrations will be indicated to the pilot with the RPM indicator. It has yellow and red marked lines to signify levels of cautionary and dangerous vibrations.
- Oil passages: there are diagonal passages drilled into the crankshaft that is connected to oilways in the crankcase. Each journal has a passage running between it and its adjacent crankpin. The oil pumped from the oilways to the main bearings provides lubrication to the crankpin.
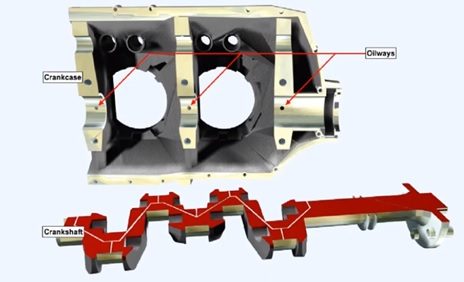
- Bearings: plain (sliding contact) bearings are used in engines with 4 or 6 cylinders in order to allow for greater reciprocating loads. Ball or roller bearings are used in larger engines. Bearings help to reduce the friction between the (metal) moving surfaces as the surfaces can slide or roll around each other rather than making harsh contact with each other. Bearings also help to reduce stress.
- Connecting rods:
They transfer the forces of combustion to the crankshaft and aid in converting the piston’s linear motion to the crankshaft’s rotary motion. It is usually made of steel with high tensile strength. It must be able to withstand both the tensile and compressive stresses imposed by the piston and its continually changing direction. The connecting rod is joined to the crank pin via a white metal shell bearing and joined to the piston via a Gudgeon pin. The part of the rod connected to the piston is called the small end while the part connected to the crankshaft is called the big end.

- Cylinder:
Its internal diameter is called a bore. They are typically made of alloy steel which is strong enough to resist combustion pressure. The cylinder is connected to the crankcase via studs and nuts which are mounted in threaded holes in the crankcase. The inner part of the cylinder pads is sometimes chamfered or tapered to allow for the placement of a big rubber O-ring around the cylinder heads. This ring serves to seal the cylinder-crankcase joint in order to prevent leakage. The other end of the cylinder is sealed by the piston.
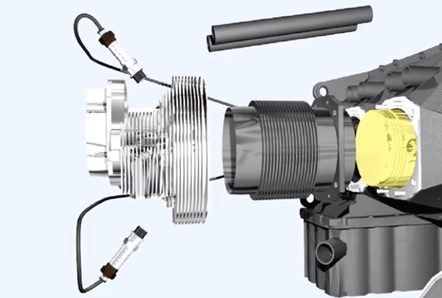
The aluminum alloys used to make the cylinder heads contribute to heat dissipation. The cylinder heads sealing one end of the cylinder provides a combustion chamber for the fuel and air mixture. They also provide housing for the valve assembly.
- Valve-operating mechanism:
This unit comprises valves, valve seats, valve springs, valve guides, rocker’s arms, push rods, camshaft and tappets. The shape of the valve and the valve seat match accurately so that they can be lapped such that full contact is attained. The valves expand the most during combustion out of all the components in the operating mechanism. For this reason and in older engines, a valve clearance must be introduced between the rocker pads and valve tips. This is so that the valve and valve seat are exactly aligned and there is no gas leakage. The valve clearance gets smaller as the engine heats up. It is measured by feeler gauges.
The valve clearance must not be:
- Excessive – otherwise, the valves will open late and close early.
- Insufficient- otherwise, the valves will close late and open early or not close at all. The latter will cause the valve to pop back into the carburetor.
In modern engines, hydraulic tappets eliminate the need for valve clearances. Under pressure, oil is supplied to the tappet such that it lengthens and takes up any clearance required. Thus, the hydraulic tappets are able to maintain contact throughout the period the engine is running. This also gives the added benefit of reduced tappet noise.
In some powerful engines, the exhaust valves are hollow so they can be filled with some sodium. This sodium aids in cooling as it melts at extremely high temperatures and then moves to a cooler part of the valve so that the temperature can be more balanced. The valve guides help to ensure the valves maintain a straight path and concentric alignment with their seats. The valve guide is typically pressed into the cylinder head.
Valve springs are made of spring steel. They make sure the valves are closed unless opened by the camshaft’s cam. They have a helical shape and are configured such that one pair of springs is connected to one valve, one of the springs being inside the other. The use of two springs per valve provides redundancy and prevents valve bounce. Springs are held compressed between the cylinder head and valve spring caps. Collets found in the grooves of the valve stem join the springs to the stem.
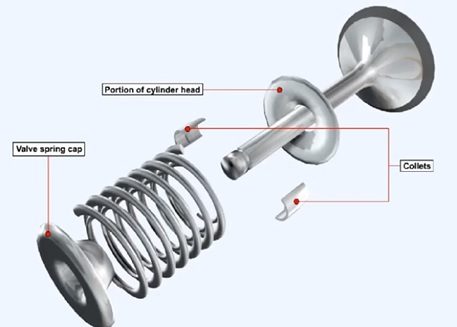
The rocker arms, one for each valve, are mounted on a shaft in the cylinder head. They are the primary means of actuating the valves. Camshafts which are driven by the crankshaft at half crankshaft speed provide the initial impulse which opens the valves. Half the crankshaft speed is used so that the valves can only open once during the 2 revolutions of crankshaft rotation. Such a speed is obtained by using a camshaft gear that has twice the diameter and number of teeth as the crankshaft gear, i.e., a 2:1 reduction gear train. The cam lobes are profiled to provide the required valve lift, duration, and timing. The tappet rides on the cam lobe and converts the profile into a reciprocating movement which is transferred to the push rods and rocker’s arms.
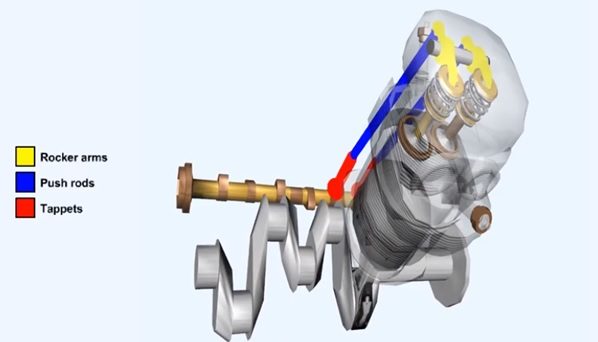
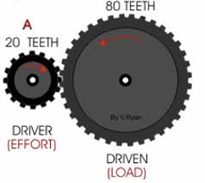
The camshaft usually has one lobe for each cylinder’s exhaust valve and one lobe with double the width for each pair of inlet valves on opposing cylinders. So in a 4-cylinder engine, there will be 6 cam lobes and in a 6-cylinder engine, there will be 9 cam lobes. The lobes are polished and carburized to obtain hard and durable surfaces.
- Piston:
It is typically made of aluminum alloy. The piston forms a sliding plug in the cylinder. There are Gudgeon bosses in the piston for housing the Gudgeon pins. There are grooves around the piston to allow for the attachment of the piston rings. The piston rings serve to prevent combustion pressure (gas) from leaking from the piston to the crankshaft, or oil from leaking into the combustion chamber. Thus, some of these rings are dubbed compression rings while some are dubbed oil control rings. The former is placed in the upper part of the piston.
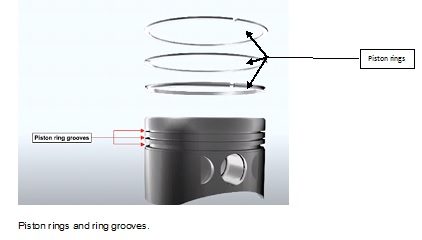
The compression rings will be forced down into their grooves when gases pass between the piston and cylinder wall. The number of compression rings fitted is determined by the amount of gas that will pass. The oil control rings throw out the oil that gets splashed into it. They also evenly distribute the oil around the cylinder bore. The rings are typically made of cast iron because it maintains their elasticity when heated and have self-lubricating properties. A malfunction with the piston rings is indicated by blue smoke (from the burnt oil) being released from the exhaust
- Ignition system: most engines have two electrically independent ignition systems which have two spark plugs for each cylinder and two engine-driven magnetos (generators). The magnetos supply electric power to the spark plugs which then deliver electric current to the combustion chamber for the purpose of igniting the fuel/air mixture. In order to prevent detonation by shortening the combustion time, the two spark plugs of a cylinder are usually made to initiate the flame at the same time. The dual ignition system also adds to the redundancy of the engine system.
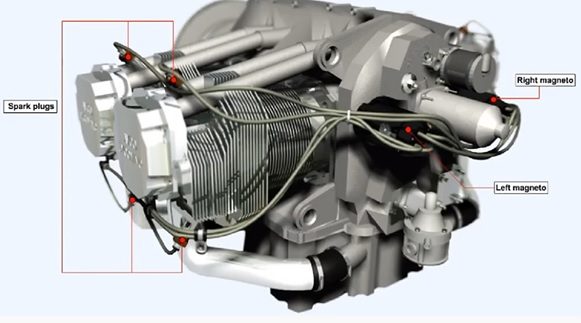
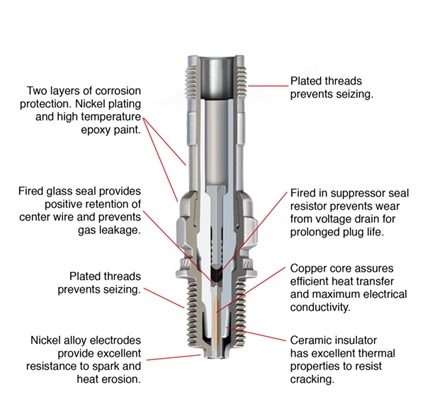
The magnetos are able to generate the high voltage needed to create the spark. A rotary switch called a distributor is found in the magneto and serves to direct the voltage to the spark plugs in the correct firing sequence.
- Starter systems:
There are different types of starters used in piston engines. They are:
- Inertia starters: their operation depends on the kinetic energy stored in the flywheel which rotates very quickly. Energy is slowly stored during an energizing process by means of a small electric motor or a manual hand crank. During the process, all movable parts of the starter are set in motion. After the starter has become fully energized, it engages the crankshaft either electrically (solenoid) or mechanically (cable). The flywheel energy is then transferred to the engine via a set of reduction gears and a torque overload release clutch.
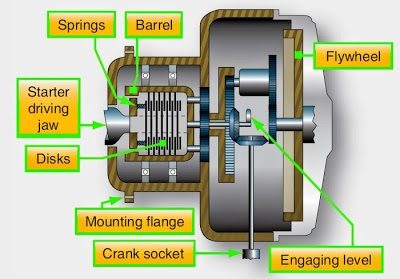
- Direct cranking electric starter- this is a popular choice for starting systems of piston engines. It provides immediate and continual cranking when energized. It comprises reduction gears, an electric motor, and an automatic engage/disengage mechanism. An adjustable torque overload release clutch operates the combination of these components. The starter motor has a nominal voltage of either 12 or 24 V and is a series wound.
The motor is able to produce a large starting torque which is transmitted to the clutch via the reduction gears. This then actuates a shaft that moves the starter jaw outward so as to engage the engine-cranking jaw before the starter jaw starts rotating. After the engine reaches a specified speed, the starter disengages automatically.
- Lubricating systems:
The lubricating systems of piston engines can be classified into the wet sump and dry sump.
The sump is placed at the end of the crankcase. In dry sump lubricating systems, the oil is pumped from the crankcase to the external tank. Additionally, the dry-sump system comprises a scavenge pump and external tubing.
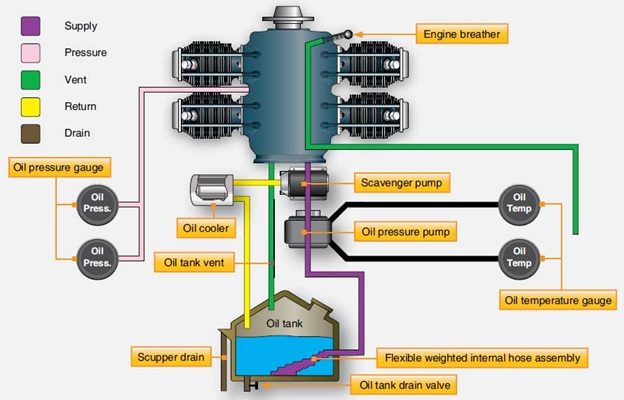
- Fuel metering units:
The carburetor is the most commonly used component for metering the engine’s incoming air and adding the required amount of fuel so as to obtain the correct fuel-to-air ratio. It sprays the fuel in a quantity suitable for the conditions the aircraft is flying in. In order to spray, it must first atomize the fuel. The spraying is then done in an evenly distributed manner so that all the cylinders have equal amounts of fuel in them and therefore, even combustion. The carburetor should also be able to stop the flow of fuel to the engine. Fuel systems will be talked about in more detail in a subsequent section.
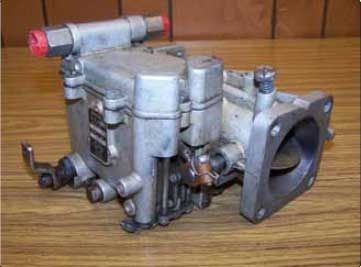
Some engines may have a fuel injection system instead. Via metal pipes, the fuel control unit is connected to the fuel manifold valve and then to the injector for each cylinder.
- Supporting systems:
They are part of the accessory housing which is securely fastened to the accessory section of the crankcase. They include oil pumps, fuel pumps, and vacuum pumps. Superchargers, tachometer generators, starter motors, and magneto ignition systems may also be fitted to the accessory housing. Additionally, the accessory housing may be able to provide power to the electrical, hydraulic, and/or pneumatic systems of the aircraft.
Operation of Aircraft Piston Engines
Piston engines operate based on a four-stroke cycle controlled by the rotation of the crankshaft. Ignition timing has a lot to do with the power delivered by the engine. It, together with valve timing, happens at specific points during the rotation of the crankshaft. These points are marked by the amount of rotation the crankshaft has done at that time.
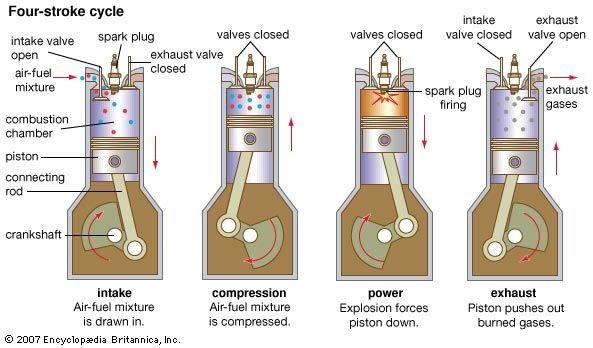
Ideally, this will be the case:
- During the induction stroke, the inlet valve opens at the top while the piston moves to the Bottom Dead Centre (BDC). Once the piston is at BDC, the inlet valve closes.
- The piston moves up and compresses the air mixture let in through the inlet valve. This is the compression stroke.
- Ignition will occur before the piston goes to start its power stroke and the ignition spark will trigger the combustion of the gases.
- The drastic increase in temperature due to combustion will be accompanied by a rise in the pressure of the gases above the piston which will force the piston down. This is the power stroke. Now with the piston at the Bottom Dead Centre (BDC), the exhaust valve opens and the exhaust gases escape against the atmospheric pressure.
- The piston then moves to the TDC once more and the exhaust valve closes. This is the exhaust stroke.
In reality, this is what happens:
- The valve and ignition timings are made different for more efficient operation. The inlet valve opens before the piston reaches the TDC (valve lead). This is necessary because the airflow has inertia so it will take some time for it to keep up with the movement of the piston.
- With this new arrangement, the air will flow into the cylinder as soon as the piston starts moving down. Since the momentum of the air will increase as the induction stroke progresses, the air will keep flowing for some time even after the piston reaches BDC and starts moving up again.
- Thus, the inlet valve will not be closed immediately after the piston gets to the BDC so that the pressure in the cylinder can match the appropriate amount (valve lag).
- The pressure rise during compression is more than the theoretical value and is further increased to the peak value once combustion is completed.
- The ignition timing must be such that the point at which there is complete combustion coincides with the piston being a few degrees above the TDC during the power stroke. This is because, at this point of maximum pressure, optimum mechanical energy can be obtained to drive the crankshaft. This mechanical energy is obtained as the piston moves back down.
- If the exhaust valve opens before the piston reaches the BDC (valve lead), what is left of the pressure will be used for exhaust scavenging.
- Now at the BDC, very little pressure is left in the cylinder. This process is termed ‘pressure scavenging’. It does not cause a significant reduction of the mechanical energy because the distance left for the piston to reach BDC is not very much at this point. Also, there will still be some pressure from the cooled and expanded gases atop the piston.
- The exhaust valve is left open (valve lag), even after the piston has completed its exhaust stroke and moves up a bit further, so the gases can scavenge the cylinder quickly using their momentum.
This change in valve timing is effective because it allows for the gases to come in and escape at periods where the piston undergoes more displacement for the same amount of angular displacement of the crankshaft. More displacement means more change in the volume of the piston so the weight of the charge entering the cylinder and the scavenging of the exhaust gases can be improved. These valve timing changes are termed ‘valve lead’, ‘valve lag’, and ‘valve overlap’.
Valve overlap occurs when the exhaust valve and inlet valve are open at the same time. As the exhaust leaves the cylinder, the pressure within the cylinder will decrease. This will encourage the gases from the inlet valve to enter the cylinder since gases tend to move from higher pressure to lower pressure. This inflow of gases will further displace the exhaust gases out of the cylinder, against atmospheric pressure. Thus, the volumetric efficiency of the engine is improved since there is a greater weight of charge in the cylinder. The valve timing for any engine is fixed, remaining unchanged even with an increase or decrease in the engine’s RPM. This is made so by the fixed positions of the lobes on the camshaft.
The air which enters the engine comprises 78% nitrogen and 21% oxygen. Oxygen is what actually burns the fuel. The nitrogen only helps to slow down the combustion so that it can be a controlled process. During combustion, the compressed charge in the cylinder is ignited by the spark from the spark plug with a frame rate of about 60 ft/s so that the temperature rise in the combustion chamber is steady and smooth.
Electronic sensors are used to measure the change in the position of the piston and cylinder’s contained volume during the engine’s operation and indicate them. A P-V diagram is produced, the area under which is the work done on the gas and is related to the power produced by the engine.
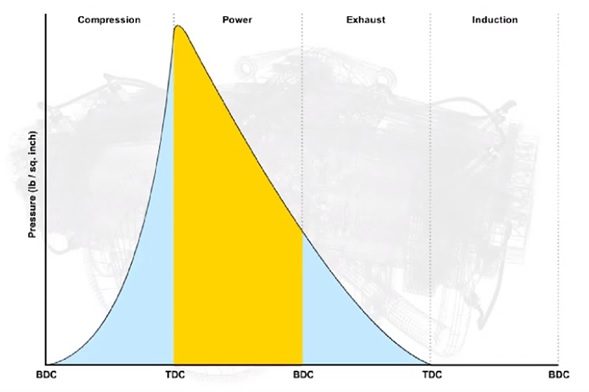
In the above diagram, the work done on the piston is denoted by the yellow area while the work done by the piston is denoted by the blue areas. Obviously, the piston does work when it compresses the gases and when it pushes out the exhaust against the atmosphere. The difference between the yellow area and the total blue area is called the Indicated Mean Effective Pressure (I.M.E.P.). The IMEP can be used to find the indicated horsepower (IHP) of the engine using the following formula
IHP = (PLANE/33000)
Where P= IMEP in psi.
L= length of stroke in ft.
A= area of the cylinder in in2
N= number of cylinders.
E= effective working strokes per minute or half of the rpm.
The actual forms of power to be concerned for the engine are brake horsepower (BHP) and friction horsepower. The latter is the amount of power required to turn the crankshaft and move the piston. The BHP is the difference between the IHP and the friction horsepower. It is the amount of power required to turn the propeller or gearbox(es).
The specific fuel consumption (SFC) or brake-specific fuel consumption (BSFC) of the engine is influenced by the engine’s design and the way the pilot operates the engine. The BSFC can be improved by opening and closing the throttle in a smooth manner, rather than abruptly.
The mechanical efficiency is the BHP divided by the IHP as a percentage. It is usually between 80-85%. The average value of the thermal efficiency of the piston engine is usually between 25-28%. The thermal efficiency can be enhanced by increasing the engine’s compression ratio. This is because when the fuel/air mixture is raised to high pressure before combustion, much higher pressure can be attained post-combustion. However, the compression ratio should not be so high that excess pressures are obtained which can lead to detonation. The compression ratio is the ratio of the cylinder’s total volume to its clearance volume, i.e., the volume left when the piston is at the TDC. The more the amount of air and fuel the engine can draw in during its induction stroke, the higher its power output will be.
Volumetric efficiency can be defined as the ratio between the volumes induced by the cylinder during the engine’s operation to the volume under standard atmospheric pressure and temperature, with the piston stationary at the bottom.
Volumetric efficiency is influenced by the following factors:
- Size of the intake manifold and the carburetor throat.
- Valve timing.
- Cylinder head design.
The greater the number of cylinders, the greater the number of power strokes for the given crankshaft angle of rotation. Consequently, a greater number of intervals means shorter intervals between power strokes. This interval is termed the firing interval. Four cylinders are the minimum number used because below that, an unreasonable firing interval will be obtained. The firing order is the order in which the cylinders fire within 2 revolutions of crankshaft rotation; it is influenced by the arrangement of the cylinders with the crankshaft. For a four-cylinder engine, the firing order can be 1-3-2-4 meaning the 1st cylinder in the line-up has its power stroke first followed by the 3rd cylinder followed by the 2nd followed by the fourth.
Types of Aircraft Piston Engines
The aircraft piston engines can be classified based on the following:
- Cylinder configuration.
- Type of drive
- Cooling method.
- The direction of rotation.
- Cylinder capacity.
- Fuel system type.
- Type of charge.
However, for the purpose of this article, we will only look at the classification according to cylinder configuration.
Generally, the more the number of cylinders in the engine, the more smoothly the engine runs. Hence, unlike in most automobiles where a small number of cylinders is used, aviation piston engines can have up to 8, 12 or even 16 cylinders. Nonetheless, some light aircraft have engines with just four cylinders.
The arrangement of the cylinders (about the crankshaft) influences the vibration in the engine and its alignment when fitted into the aircraft.
The different cylinder configurations are:
- In-line and horizontally opposed: they are typically used in lighter aircraft piston engines. Horizontally opposed is the more preferred. In-line engines can also have their cylinders inverted. 4- and 6- cylinder horizontally opposed engines are especially used in General Aviation Aircraft (GAA). They typically use hydraulic tappets.
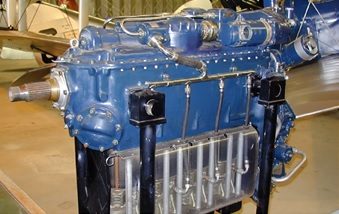
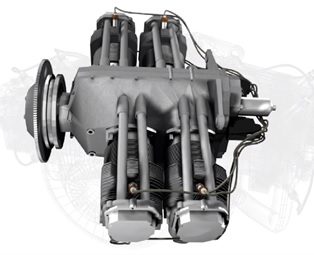
Both types of four-cylinder engines make use of four-throw crankshafts. Both types of six-cylinder engines as well as V12 engines make use of six-throw crankshafts.
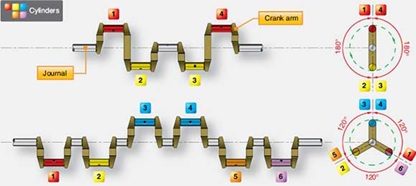
In-line engines have poor dynamic balance and are a bit hard to package, however, they are beneficial in that they run smoothly and deliver power efficiently. Horizontally opposed engines are even better in terms of power delivery and smoothness but are even more stressful to package.
- V configuration: For more powerful light aircraft engines, V configuration is preferred for the cylinders. It typically has either 8 or 12 engines, i.e. 4 or 6 pairs of V’s. However, a V16 engine configuration has also been implemented in some aircraft. V12 engines are more dynamically balanced than V8 engines. A V configuration allows the packaging of the engine to be slimmer meaning it can be more easily streamlined into the fuselage or engine nacelles of the aircraft. This is of prime importance to the aerodynamics of the aircraft as drag would be reduced.
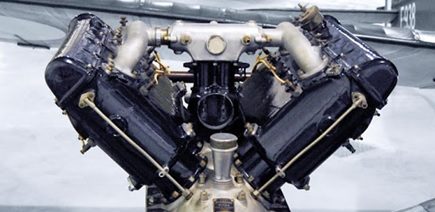
V engines may have cross-plane or flat-plane crankshafts. The former fire unevenly and are therefore more dynamically balanced and smooth. The latter fire evenly and are therefore less balanced. Cross-plane engines deliver more power and have more torque than their flat-plane counterparts, however, they tend to be heavier since counterweights must be added to make them statically balanced.
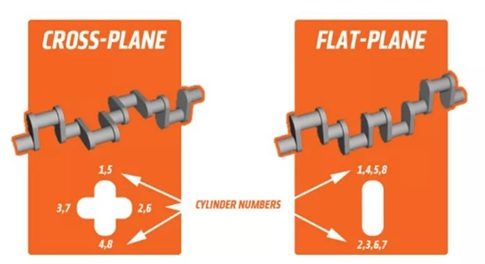
- Radial configuration: this arrangement of cylinders around the crankshaft allows for a larger frontal area. This induces more drag but gives shorter and lighter exhaust than equivalent power in-line engines. Radial piston engines were a popular choice before the advent of turboprop engines. The crankshafts used in radial engines look quite different from the normal crankshafts, although, they have the same basic parts. They can either have one throw, two throws, or four throws depending on the corresponding number of rows of the engine. Dampers and counterweights are added to them so as to reduce vibration. A single-throw crankshaft has two main bearings, one for each end. In radial engines, a sump may be placed at the bottom of the crankcase nose.
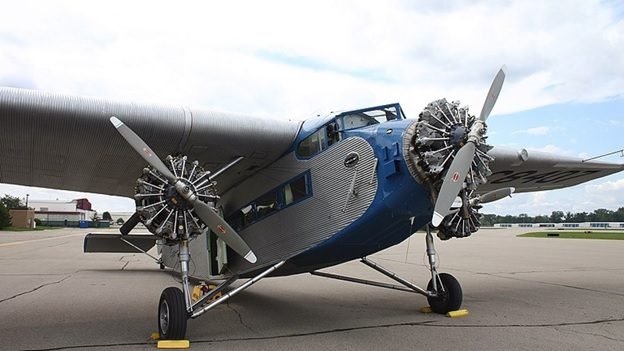

- W-, X- and H- formation engines have also been developed in the past.
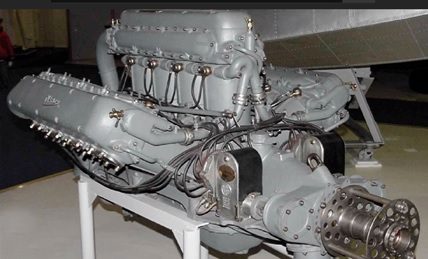
Conclusion
It is clear that engines are not just simple components, but rather elaborate systems. Many other systems contribute to the safe, efficient, and powerful (if need be) operation of the engines. Failure of these supporting systems will have great adverse effects on the engine and can even destroy the engine. We can also see that piston engines have a wide variety of configurations based on their various systems. The choice piston engine type depends on the application it is to be used for.
References.
- 2018. Aviation Maintenance Technician Handbook-Powerplant Volume 1. [ebook] FAA. Available at: <https://www.faa.gov/regulations_policies/handbooks_manuals/aircraft/media/FAA-H-8083-32-AMT-Powerplant-Vol-1.pdf>
- YouTube. 2017. ATPL Training Videos / Piston Engines – Youtube. [online] Available at: <https://www.youtube.com/playlist?list=PLthUARlELoUX6iMiZ_XGnFsErILAR7MN->