Steps to Take Reading Of Dial Gauge During Machine Alignment

After the dial gauge is firmly mounted on the shaft of the machine to be rotated then four locations at the circumference of the shaft or coupling of the stationary machine are required for taking the readings for alignment.
These four locations are at the 90-degree rotation of the shaft. Before any readings to be taken the dial indicators must be set.
Adjust the dial gauge in such a way that the sensor of the dial gauge is slightly pressed against the circumference of the coupling.
Rotate the machine shaft through an entire 360 degree and verify that the indicator sensor tip is in complete contact with the shaft.
Now when the indicator is at the top location reset the indicator to display zero.
This is achieved by rotating the outer bezel of the indicator until the dial face, which is attached to the bezel, shows “0” under the needle.
Collect the data by rotating the machine shaft in 90-degree increments and noting the dial indicator readings with their signs (- or +) at Top, Right, Bottom and Left locations.
If only one dial indicator setup is available, the dial gauge mounting arrangement must be relocated to the other coupling or shaft of the stationary machine and the sweep should be repeated.
Remember that all readings should be collected while observing from the stationary machine to the movable machine to maintain right and left consistently.

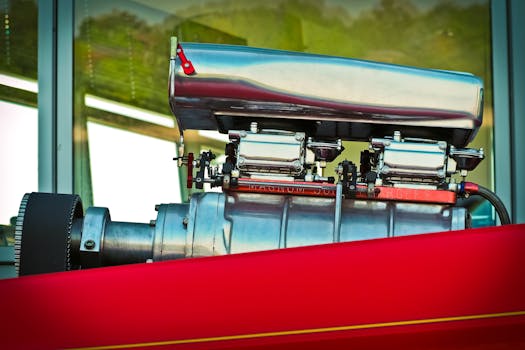
When the dial gauge is mounted on a stationary machine and readings are taken on the machine to be moved then change the sign of readings so obtained. +ve sign to be made –ve sign to be made +ve.
Accuracy verification each time the dial gauge is rotated to the top location it should display a reading of zero.
If it does not then something has moved during the rotation. Correct the problem and start again.
Another test, which can be performed as the data is collected, is to verify that the sum of the top and the bottom readings should equal the sum of the left and right readings.
While taking dial gauge reading at the bottom portion of the shaft or coupling, the value of sag must be taken into account.
Actual dial gauge reading at the bottom of the coupling (6 “0” clock position) = dial gauge reading – {-(2 sag)}
Assuming sag = 0
Top + Bottom reading = 0 + 10 = +10
Right + Left reading = -12 + 22 = +10